gb2 Ventures Services
Total Molding Performance
Learn how gb2 Ventures can fully support your project from concept to completion. We provide concept and CAD design, prototyping and 3D printing, DFM and mold flow analysis, tooling, injection molding, blow molding, low-pressure structural foam molding, resin distribution, packaging and consulting.
We can meet your company’s specific requirements because we are well versed in various industries, such as medical devices, agriculture, automotive, sporting goods, home and garden, electronics, semiconductors and industrial. Our high-quality plastic molding solutions can meet those strict regulatory standards and any industry best practice.
Our broad network of manufacturing partners across the US and Mexico can meet those strict regulatory standards and any industry best practice
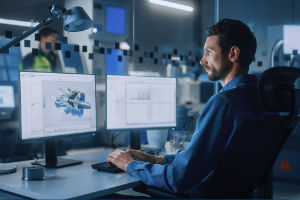
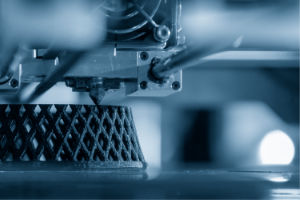
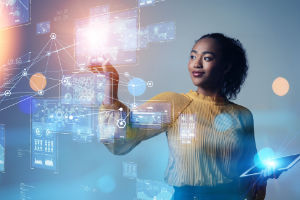
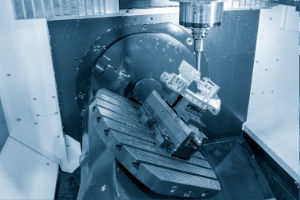
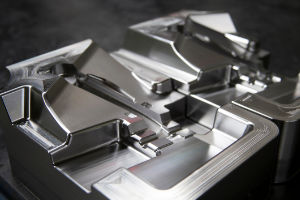
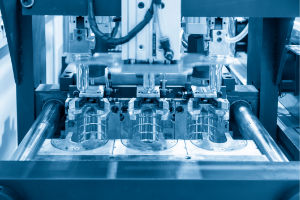
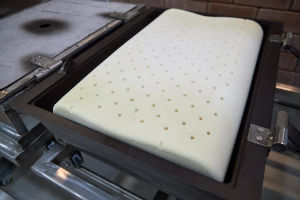
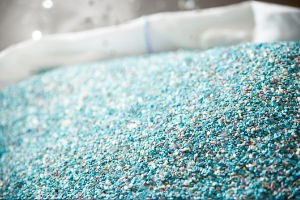
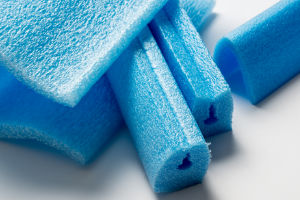
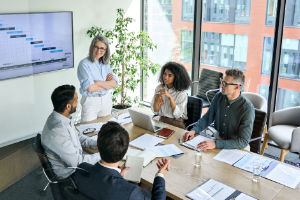
Frequently Asked Questions
Blow molding is used for hollow parts, many times bottles and containers, such as shampoo, detergent and oil bottles. Milk Bottles, coolers, and gas tanks are more examples of blow molding. Injection Molding requires highly engineered molds to process a large range of sizes and volumes and are typically constructed of steel. They must withstand much higher processing pressures as compared to blow molding which for the most part uses aluminum molds. Creating a mold is required for custom applications in both blow molding and injection molding..
The pellets of resin are heated up to the proper melting temperate specific for the resin and are pushed through the screw and barrel. They are extruded out the die head forming a molten hot hollow tube called a parison. The 2 halves of the blow molds are then closed around the parison and air is blown into the mold forcing the plastic to stretch and take the shape of the mold. Air continues to blow while chilled water circulates through the mold cavities cooling down the part. When the cycle is completed, the mold halves open and the parts move on to the next downstream steps, typically onto a conveyor.
The pellets of resin are heated up to the proper melting temperature specific for the resin and are injected under high pressure through the screw and barrel into the nozzle and through the gate system of the mold. The pressure forces the molten hot plastic to fill the cavities of the mold while chilled water runs through the mold cooling the part and taking its shape. When the cycle is completed, the mold opens and the ejector system pushes forward ejecting the part from the mold. At this point, the parts either fall onto a conveyor or are removed via robot.